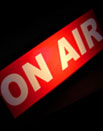
Così Emerson Network Power ha riorganizzato i processi aziendali con i partner, riducendo dell’80% le giacenze di magazzino.
Con una presenza globale sul territorio e un team di oltre 6.000 persone, Emerson Network Power concentra le attività produttive dei propri Ups per il Vecchio Continente in due plant: a Piove di Sacco, nei pressi di Padova, e a Nove Mesto, in Slovacchia. Per i modelli Micro e Small, le attività direzionali sono condotte dalla sede di San Giuliano Milanese. Il 50% degli approvvigionamenti proviene dal Far East, da aziende del gruppo e da fornitori esterni.
A partire dal 2000, la società ha riorganizzato i propri processi aziendali. «La continua oscillazione del mercato – esordisce Mario de Leva, Supply chain manager di Emerson Network Power -, ci ha spinto a cercare metodologie di lavoro volte a snellire lo svolgimento delle attività produttive e di servizio ai clienti finali». La società si è allora proiettata verso il concetto di lean manufacturing, insieme di strumenti e tecniche finalizzati a prevenire gli errori umani nell’operatività e a eliminare gli sprechi. «Una simile revisione dei processi d’impresa ha comportato il coinvolgimento delle aree logistiche – prosegue il manager -. La complessità della catena di fornitura, in quanto i nostri partner sono distribuiti a livello locale, nazionale e internazionale, ha richiesto un aggiornamento tempestivo dei dati nei sistemi informativi». Si è presentata dunque la necessità di scegliere uno strumento informativo di rapida implementazione e dal semplice utilizzo, che consentisse l’integrazione dei partner più strategici, anche quelli del Far East.
«I paesi principali sono Taiwan e Cina – esordisce Marina Bossi, Micro & Small Ups logistic manager di Emerson Network Power -. Dalla sede di San Giuliano Milanese vengono inviati gli ordini di acquisto; la merce viene trasferita, in circa quattro settimane, via mare al nostro hub olandese. Da qui raggiunge il cliente finale. Il ritiro della merce ordinata era effettuato con container che possono contenere 3.000 unità, talvolta con un chiaro avanzo di spazio». Una rigidità di gestione che andava sorpassata rendendo la comunicazione tra l’azienda e i fornitori orientali più semplice e trasparente per ottenere un livello di dettaglio per unità anziché per container e avere un carico di magazzino più lineare.
Nel 2001 la società ha adottato Manem. «La soluzione di Joinet ci è sembrata rispondente alle nostre esigenze, in quanto ci consente di generare simultaneamente e automaticamente un ordine di produzione alla fabbrica e una richiesta di commessa ai fornitori coinvolti nella realizzazione di quel particolare prodotto», commenta de Leva. Dopo un iniziale progetto pilota, sono stati implementati moduli aggiuntivi, come forecasting, invoicing e backlog, e integrati complessivamente 23 fornitori (dall’ottobre 2004, anche quelli del Far East). «Quando si genera un work order – prosegue il manager -, il codice prodotto viene scomposto in codici componenti inviati ai fornitori interessati attraverso un’informazione di backlog, in contemporanea alla fabbrica incaricata della produzione. Il ciclo d’ordine è interamente gestito. In particolare, il nostro sistema Erp interfacciato con l’hub olandese, registra automaticamente ogni utilizzo della merce ordinata in consignment stock e trasmette a Manem i dati in modo da consentire ai fornitori di fatturare settimanalmente gli effettivi consumi».
Al miglioramento nella gestione della supply chain in termini di velocità e sicurezza si è aggiunta la riduzione degli errori umani, grazie all’automatizzazione di molte operazioni, come per esempio il download dei documenti di trasporto. Una migliore qualità nella comunicazione consente all’azienda di avere sempre ben visibile lo stato delle merci in transito e in consignment, fino a ottenere l’auspicata possibilità di caricare contabilmente a magazzino esclusivamente le singole unità necessarie a coprire gli ordini in spedizione. Una flusso continuo a magazzino, dunque, che equivale ad una riduzione dell’80% in due mesi circa del valore delle giacenze, con un impatto visibile sul bilancio e nessuna penalizzazione delle esigenze di disponibilità di scorte.